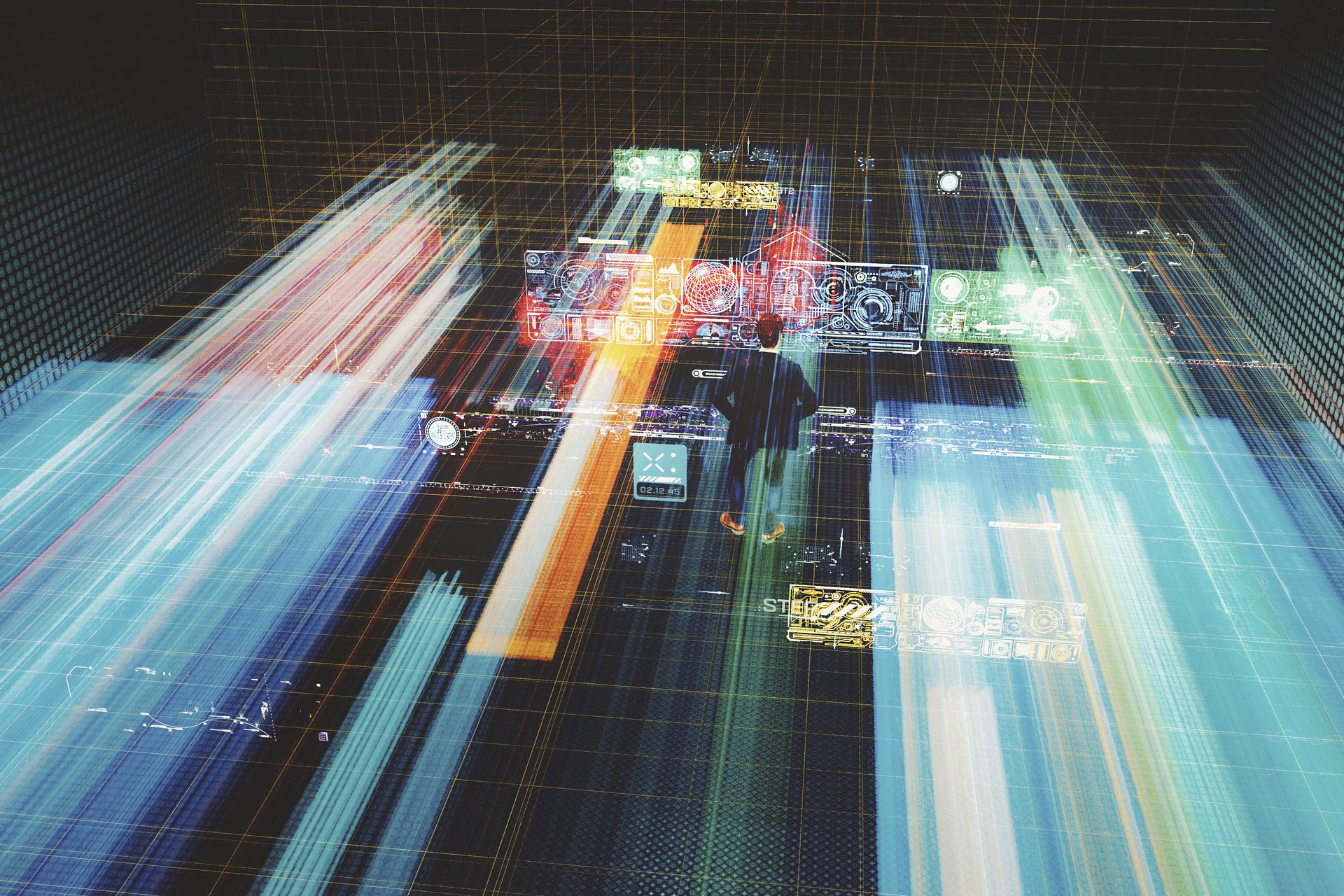
What is machine data used for? An explanation of how added value can be created from measured values
The answer is as simple as it is cryptic: DIKW.
What does the DIKW pyramid represent?
The DIKW pyramid is a hierarchical model that describes the transformation from data through information and knowledge to wisdom. It is worth taking a closer look at the levels of the DIKW model and how they explain the creation of value from data in industrial companies:
- Data: Raw data is the basis of the model. These are context-free values that are not very useful in the first step. For example, this could be the value "5 minutes". Without further context, this value is not meaningful and does not provide any insights into causes or effects.
- Information: Information is created by contextualizing the data. This means that a context is assigned to the value, for example the type of time interval, the exact machine and the time. For example, the data record "5 minutes" becomes the information "Machine X had a standstill of 5 minutes on Tuesday at 2:30 pm". This information already allows us to better understand the event, but the exact reason and consequences are still unclear.
- Knowledge: Knowledge is created when several pieces of information are brought together and analyzed in order to identify patterns or correlations. Knowledge makes it possible to draw well-founded conclusions and make decisions. For example, the system could show that machine X has a downtime of around 5 minutes every Tuesday at the same time. The combination of this information allows the conclusion to be drawn that the downtime is systematic. This can lead to the knowledge that maintenance needs to be adjusted or the load on the machine needs to be checked. On the other hand, the combination with the information "Order Y was loaded on the machine at the beginning of the downtime" could lead to the knowledge that maintenance or a check of the machine load is necessary. This in turn could lead to the knowledge that the downtime was a setup process.
- Wisdom: Wisdom is the highest level of the pyramid and requires experience and contextual knowledge in order to develop long-term decisions and strategies. Here, the knowledge and results from the analyses are embedded in larger contexts and used for future scenarios. For example, wisdom might mean not only fixing the immediate cause of the downtime, but also developing a long-term strategy on how to avoid similar problems in the future. This means establishing preventative maintenance processes for these and similar machines or looking at alternative solutions for operations to increase efficiency in the long term. Such strategic decisions usually require human expertise and a deep understanding of the production environment.
The DIKW pyramid therefore helps, for example, to trace the path from logged time intervals to strategic decisions on maintenance strategies.
How does machine data become added value in practice?
Extensive automation of the DIKW pyramid is essential in order to make efficient use of the wealth and frequency of modern machine data. In a modern production plant, it is not uncommon for a machine to record and update several hundred data points per second. In order to generate valuable knowledge from this flood of data, sophisticated systems are required that filter and process the data intelligently and present it in a clear and concise form. The CANCOM Industrial Data Platform offers such a possibility. Each recorded event is automatically provided with a time stamp and a place of origin in order to turn data into information as close to the source as possible. With the help of rules, downtimes can be recognized and classified in the CANCOM Industrial Data Platform. Such automated solutions ensure that relevant information is available quickly and without manual effort. Based on this clean and consistent database, algorithms from the field of artificial intelligence can be used for pattern recognition. CANCOM's solutions therefore enable companies to use machine-generated data to analyze production downtimes. In addition, there are many other use cases, such as automated quality control or energy monitoring and management, for which the CANCOM Industrial Data Platform forms a solid basis.
New perspectives: The role of real-time data in decision-making
An often underestimated aspect of the use of machine data is the importance of real-time information for decision-making in production. While the DIKW pyramid describes the gradual transition from data to wisdom, real-time data offers a dynamic addition that is particularly crucial in highly networked and automated production environments.
Real-time data makes it possible not only to react to historical patterns and findings, but also to respond proactively to current events. For example, anomalies or unexpected deviations from normal operating parameters can be detected immediately, allowing early intervention. This reduces downtime and increases efficiency as problems can be resolved before they have a major impact.
The use of real-time data in the CANCOM Industrial Data Platform makes this possible:
- Predictive maintenance: by monitoring machine conditions in real time, maintenance intervals can be optimized and unplanned downtime avoided.
- Energy optimization: Real-time data on energy usage can help to make consumption more efficient, for example by making adjustments during peak loads.
- Adaptive control: Production processes can be dynamically adapted to changing conditions, whether due to fluctuations in material quality or short-term changes in demand.
Real-time data expands the possibilities of the DIKW pyramid by bridging the gap between the analytical depth of past data and the operational need for immediate decisions. This addition not only enables companies to act more efficiently, but also to react agilely to unpredictable challenges - a significant advantage in modern industrial production.
The CANCOM Industrial Data Platform therefore enables the automation of the first three steps of the DIKW pyramid and thus helps to use machine data for operational, tactical and strategic decisions. In most cases, this data already exists in production, but it is not being used profitably. In this respect, the CANCOM Industrial Data Platform can harness unused potential for data-driven optimization and help production operations to become more competitive.
[1] See, for example, Rowley, 2007. https://doi.org/10.1177/0165551506070706.